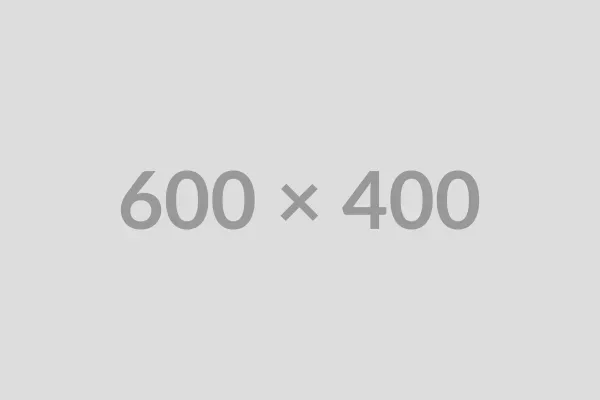
Date: July 22, 2024
Mobile warehouse management
Enhancing Efficiency with Mobile Warehouse Management: A Modern Approach
In the fast-paced world of warehousing and logistics, the ability to manage inventory efficiently and accurately is crucial. Mobile warehouse management solutions are transforming how warehouses operate by leveraging mobile technology to streamline operations, improve accuracy, and enhance productivity. In this blog post, we’ll explore the benefits of mobile warehouse management, key features to look for, and best practices for implementing a mobile solution in your warehouse.
1. What is Mobile Warehouse Management?
Defining Mobile Warehouse Management
Mobile warehouse management involves using mobile devices, such as smartphones, tablets, and handheld scanners, to manage and streamline warehouse operations. These mobile solutions integrate with warehouse management systems (WMS) to provide real-time access to inventory data, facilitate transactions, and optimize workflows.
2. Benefits of Mobile Warehouse Management
a. Increased Efficiency
Mobile warehouse management tools enable warehouse staff to perform tasks such as inventory checks, order picking, and stock replenishment on the go, reducing the need for manual paperwork and streamlining processes. For more insights on improving warehouse efficiency, visit scanqr.ai.
b. Real-Time Data Access
With mobile solutions, warehouse personnel can access real-time inventory data, track shipments, and update information instantly, leading to more accurate and timely decision-making. Explore how mobile inventory systems can transform your operations.
c. Improved Accuracy
Mobile devices equipped with barcode scanners or RFID technology reduce the likelihood of errors in data entry, inventory tracking, and order fulfillment, enhancing overall accuracy. Learn more about barcode scanning solutions on our website.
d. Enhanced Productivity
By enabling tasks to be performed directly from the warehouse floor, mobile solutions minimize downtime and optimize the workflow, leading to increased productivity and faster order processing. Discover how productivity tools can enhance your warehouse operations.
e. Better Visibility
Mobile warehouse management provides real-time visibility into inventory levels, order statuses, and warehouse operations, allowing for more effective monitoring and management. For more on improving visibility, check out our inventory visibility tools.
3. Key Features of Mobile Warehouse Management Solutions
a. Barcode Scanning and RFID Integration
Mobile devices equipped with barcode scanning or RFID capabilities enable efficient tracking and management of inventory items, reducing manual entry and improving accuracy. Explore our barcode and RFID integration solutions.
b. Real-Time Inventory Updates
Mobile solutions should provide real-time updates on inventory levels, order statuses, and other critical data, ensuring that information is current and accurate. Learn more about real-time inventory tracking.
c. Task Management
Features for task management, such as order picking, packing, and replenishment, allow warehouse staff to receive and complete tasks directly from their mobile devices. For more on optimizing task management, visit scanqr.ai.
d. Data Analytics and Reporting
Integrated analytics and reporting tools provide insights into warehouse performance, inventory levels, and operational metrics, helping to drive data-driven decisions. Discover our data analytics solutions.
e. Integration with WMS
Mobile solutions should seamlessly integrate with existing warehouse management systems (WMS) to ensure smooth data flow and operational continuity. Learn about WMS integration options.
4. Implementing Mobile Warehouse Management: Best Practices
a. Assess Your Needs
Evaluate your warehouse operations to determine specific requirements and objectives for implementing a mobile warehouse management solution. Identify key areas where mobile technology can improve efficiency and accuracy. Start by exploring our warehouse management assessment guide.
b. Choose the Right Solution
Select a mobile warehouse management solution that aligns with your operational needs and integrates well with your existing WMS. Consider factors such as device compatibility, ease of use, and feature set. Visit our solution selection guide for more insights.
c. Train Your Team
Provide comprehensive training for warehouse staff to ensure they are comfortable using mobile devices and understanding the new processes. Effective training is crucial for a smooth transition and maximizing the benefits of the technology. Explore our training resources.
d. Monitor and Optimize
Regularly monitor the performance of your mobile warehouse management solution and gather feedback from users. Use this information to identify areas for improvement and make necessary adjustments to optimize the system. Learn about our performance monitoring tools.
e. Ensure Security
Implement security measures to protect sensitive data and ensure that mobile devices are secure. This includes data encryption, access controls, and regular software updates. For more on data security, visit our data security solutions.
5. Challenges and Considerations
a. Device Management
Managing and maintaining mobile devices can be challenging, especially with a large fleet. Ensure that devices are regularly serviced and updated to avoid disruptions. Explore our device management solutions.
b. Connectivity Issues
Reliable network connectivity is essential for real-time data access. Address potential connectivity issues by evaluating network infrastructure and ensuring coverage throughout the warehouse. Learn more about network connectivity solutions.
c. Integration Complexity
Integrating mobile solutions with existing WMS and other systems may require careful planning and coordination. Work with technology partners to ensure seamless integration and data flow. Visit our integration planning guide.
6. Case Studies in Mobile Warehouse Management
a. Example 1: Retail Warehouse Transformation
A retail warehouse implemented a mobile warehouse management solution to improve order picking and inventory tracking. The result was a significant increase in order accuracy, reduced processing times, and enhanced overall efficiency. For more case studies, visit our case studies section.
b. Example 2: Manufacturing Facility Optimization
A manufacturing facility adopted mobile technology to streamline inventory management and maintenance processes. The mobile solution enabled real-time tracking of parts and tools, leading to reduced downtime and improved operational performance. Learn more in our manufacturing case studies.
7. Tips for Success
a. Start Small
Begin with a pilot program to test the mobile solution in a specific area of your warehouse before a full-scale rollout. This allows you to identify and address any issues early on. Visit our pilot program guide for more tips.
b. Foster User Adoption
Engage warehouse staff in the implementation process and encourage feedback. Address any concerns and highlight the benefits of the new technology to promote adoption. Learn more about user adoption strategies.
c. Stay Updated
Keep your mobile warehouse management solution and devices up-to-date with the latest software and security patches to ensure optimal performance and protection. Explore our update management solutions.